
Everything you need to know about PEI/ULTEM® for 3D printing
Source: 3dnatives.com
In recent years, the use of high performance thermoplastic materials has become increasingly important in the 3D printing industry, as the technology is moving from rapid prototyping to the production of finished parts. As a result, the requirements for 3D printing materials have increased, and high-performance thermoplastics are becoming increasingly common. Their properties make them a cost-effective alternative to some metals, and they are popular in many industries such as aerospace and medical. Within this family we find polyaryletherketone (PAEK), which can withstand high temperatures and which you may know as PEEK or PEKK. There is a much cheaper alternative, polyetherimide (PEI), an amorphous material better known by the trade name ULTEM®. Available as a filament for FDM 3D printers, it is compatible with some machines, including those of Stratasys. Let's review together the main features of the ULTEM.
PEI was developed in the 1980s by Joseph G. Wirth and commercialized by General Electric's Plastics Division under the name ULTEM. In 2007, the company sold its plastics business to Saudi Basic Industries Corporation (SABIC), which then reclaimed the patent. Although ULTEM® was embraced by many industries due to its mechanical properties, it only became suitable for mass production with the development of high-performance FDM/FFF printers: the machine's extruder must be heated to very high temperatures to melt the thermoplastic.
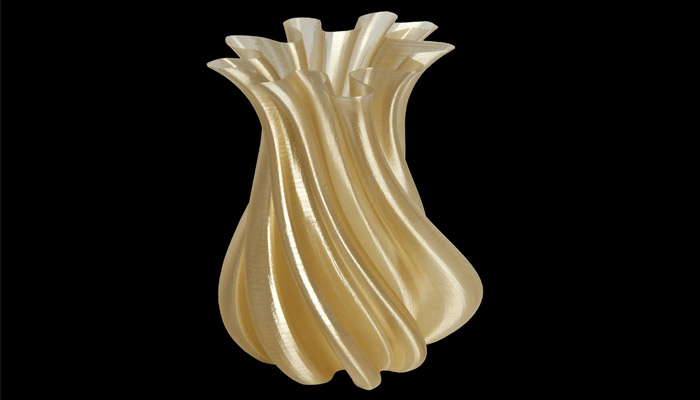
ULTEM/PEI Production and Characteristics
ULTEM® is a family of amorphous thermoplastic materials based on polyetherimide (PEI). One of its key features is its flame retardant properties: high flame resistance, low smoke generation and low toxicity. These properties are reflected in excellent results in FST (Flame, Smoke, Toxicity) tests. ULTEM® is highly resistant to high temperatures, with a Relative Thermal Index (RTI) up to 180°C. ULTEM is also characterized by high strength, stiffness and dimensional stability, good creep resistance and high chemical resistance. The different ULTEM grades also have a high strength-to-weight ratio and can even replace some metals due to their mechanical properties and high degree of processability. These materials are available in a range of transparent and opaque colors. ULTEM materials maintain their strength and resist stress corrosion cracking when exposed to automotive and aviation fluids, aliphatic hydrocarbons, alcohols, acids and weak aqueous solutions. ULTEM® 1010 has high tensile strength and durability. It is biocompatible and NSF 51 certified for food contact. It can also withstand steam sterilization.
There are also ULTEM copolymers, which can withstand even higher temperatures and accommodate different chemical and elasticity requirements. SABIC has also launched a renewable range certified by ISCC+. These ULTEM grades, made from waste and residues, offer the same high performance and processability as those made from fossil fuels. By mid-2023, renewable ULTEM materials will represent more than a quarter of SABIC’s ULTEM offerings.
SABIC currently offers 140 grades of ULTEM®. Of particular note is ULTEM™ 9085 CG, used in aerospace sector for the interiors of the cabins, but also in the railway sector. ULTEM HU1010 is used for medical devices and pharmaceutical applications because it is biocompatible.
ULTEM/PEI in 3D printing
Temperature management is essential when printing ULTEM®. The chamber temperature must always be monitored, otherwise irregularities can appear and layer adhesion can be affected. The glass transition temperature, at which an amorphous polymer changes from a hard/glassy state to a soft/rubbery state and back again, is very high for ULTEM, reaching 217°C for ULTEM1010 (185°C for ULTEM9085). For best results, the print chamber temperature should be slightly lower than the glass transition temperature. This ensures that parts are the correct size and that their mechanical properties are maintained. Once printing is complete, the print chamber should be cooled slowly and evenly, so that the part cools gradually.
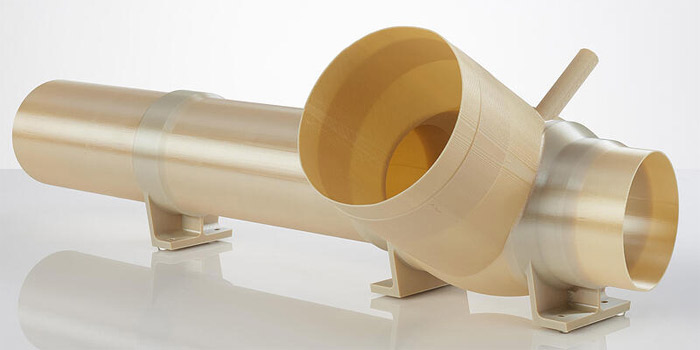
A 3D printed part used on a space launcher (Credit: Stratasys)
Compared to PEEK, PEI is usually cheaper. It is a material that has the advantage of being certified for a variety of aerospace applications, meeting highly standardized requirements. However, PEI has lower impact and temperature resistance.
ULTEM/PEI Applications
As mentioned, PEI is widely used in the aerospace industry, especially ULTEM® 9085 for the characteristics mentioned. The material is also used in the automotive, medical and food industries, especially in the design of kitchen utensils, but also in general tooling, for the design of molds, jigs or various fasteners. The Bombardier company, for example, uses this material for the production of customized tools, for the customization of components for its production lines and for the production of finished parts for its trains.
Manufacturers and prices
Finally, as far as manufacturers are concerned, SABIC is today the only one to provide the raw material, in the form of resin or foam. The company produces its own filaments for additive manufacturing: historically they were only compatible with the Stratasys range of machines, but in recent years SABIC has entered into other partnerships, such as the one with Roboze, which can print ULTEM™ AM9085F filament. Some manufacturers offer their own filaments, such as KIMYA, 3DXTech or 3D4Makers.
In addition, SABIC has also launched a support filament, AMS31F, which is easier to remove than other support materials that often need to be heated. This allows the part to retain all its mechanical properties and saves the user valuable time.
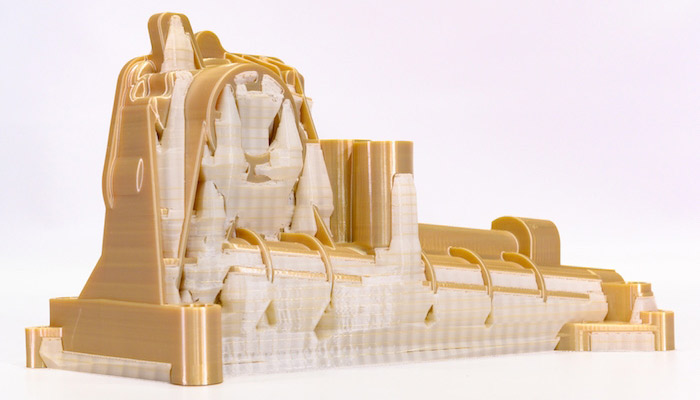
SABIC has developed a 3D printing substrate for ULTEM.
As for the price, PEI is less expensive than PEEK: it costs around 150 euros per kg compared to at least 300 euros for the same quantity of PEEK. It is a material that has the advantage of being certified for various aerospace applications, responding to highly standardized requirements. However, it is less resistant to impacts and temperatures than PEEK.