
Selective Laser Sintering (SLS): Everything You Need to Know
Source: 3dnatives.com
Selective laser sintering (SLS) is one of the technologies used in 3D printing. How does this technology work? What materials can be used? We tell you everything below!
The development of Selective Laser Sintering or SLS technologies began in the 1980s. Dr. Carl Deckard and Dr. Joe Beaman of the University of Texas at Austin (USA) developed the basis of powder bed fusion technologies. These technologies are capable of manufacturing products with multiple materials, from polymers to metals, using a laser. When we refer specifically to SLS technologies, we are talking about plastic polymers, mainly nylon. However, in recent years things have changed.
Carl Deckard and Joe Beaman patented selective laser sintering. They were also involved in the creation of DTM Corporation, now part of 3D Systems (since 2001). Since then, several companies have emerged specializing in powder bed fusion techniques, including Farsoon Technologies, which specializes in SLS. Finally, it should be noted that a process similar to SLS was invented and patented in 1979 by RF Housholder, but was never commercialized.
How does selective laser sintering (SLS) work?
Before printing, the object to be printed is designed using CAD software (e.g. CATIA, SolidWorks, ProEngineer). This model will then be sent to a 3D printer in a digital format (STL file). Printing occurs layer by layer, from molten powders, thanks to the temperature generated by a CO2 laser.
To start the process and prepare the In the SLS 3D printer, the powder bed and build plate are heated to a temperature below the melting temperature of the polymer powder (1). The first layer of powder is deposited on the print plate (2). Then, a CO2 laser selectively sinters the polymer particles into the desired shape. The entire cross-section of the component is scanned by the laser, so that the powder solidifies (3). When the layer is complete, the plate moves down and the surface of the platform is coated with material once again. The process is repeated until the part is complete (4).
After printing, the parts are completely covered in powder. The print chamber must cool down before the cleaning and post-processing phases can begin. Cooling can take up to 12 hours. The parts are then cleaned with compressed air or another cleaning technique and are ready for use or further processing.
Materials for Selective Laser Sintering
This technology allows the production of objects using a wide range of materials, although the SLS process mainly uses plastic polymers. The most common is polyamide PA 12, commonly known as nylon 12. However, the technology can also produce objects with polypropylene, Alumide, Carbonmide, PEBA, PA 11 and PEEK. It is also possible to add fibers of other additives to the materials, such as carbon fibers, glass or aluminum, thus improving the mechanical properties of the parts.
Most of the initial uses of this technology have been related to prototype development. However, as materials become stronger and SLS 3D printers become more affordable, this is changing and the trend is towards final part production.
Actors and developments
SLS technology is used in various fields: design, automotive, aerospace, engineering. Until a few years ago, the main manufacturers of selective laser sintering 3D printers were 3D Systems and EOS GmbH. The latter was the only manufacturer to include SLS machines capable of printing with high-performance thermoplastics such as PEEK. Since 2014, the patent for this technology has been issued, so many players have emerged in the sector. From new companies such as Natural Robots and its VIT machine to well-known brands such as Formlabs and its new Fuse 1. This should democratize these technologies and bring them closer to companies operating in the sector.
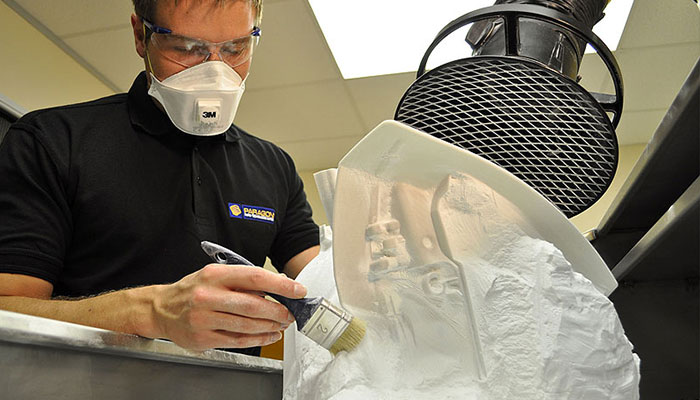
Photo credits: Paragon Rapid Technologies Limited
Finally, in the following video, the Xometry team explains the technology in detail: