
Leitfaden zu Materialien für den 3D-Druck: Verbundwerkstoffe
Quelle: 3dnatives.com
Verbundwerkstoffe entstehen durch die Verbindung von mindestens zwei verschiedenen Materialien. Das eine dient als Matrix und dient dem Erhalt der Struktur, das andere sorgt als Verstärkungsmaterial für zusätzliche Eigenschaften. Das Ziel eines Verbundwerkstoffs besteht darin, dem Ausgangsmaterial zusätzliche Eigenschaften hinzuzufügen und gegebenenfalls dessen kritische Eigenschaften zu neutralisieren. Durch die Hinzufügung der Eigenschaften des jeweiligen Verstärkungsmaterials zum Grundmaterial erhält dieses bessere mechanische Eigenschaften, eine andere Farbe, Flammwidrigkeit, Stabilität, Belastbarkeit usw. Verbundwerkstoffe werden weltweit durch ihre Materialeigenschaften (metallisch, mineralisch, keramisch, organisch) oder durch ihre Geometrie unterschieden. Aufgrund ihrer geometrischen Eigenschaften werden sie unterschieden in:
- Partikelkomposite
- Faserverbundwerkstoffe (kurz, lang oder durchgehend)
- Schicht- und Strukturverbundwerkstoffe
Besonders beliebt sind Faserverbundwerkstoffe. Am weitesten verbreitet auf dem Markt ist wahrscheinlich Kohlefaser, gefolgt von Glasfaser, die ebenfalls am häufigsten verwendet wird additive Fertigung.
Eigenschaften von Verbundwerkstoffen im 3D-Druck
Verstärkte Materialien für die additive Fertigung basieren häufig auf Nylon, aber auch ABS, PLA, PC und PETG. Derzeit sind die im 3D-Druck am häufigsten verwendeten Verbundwerkstoffe Kohlefasern, Glasfasern und Kevlar-Aramidfasern (PPD-T). Diese Materialien bieten Vorteile für die Herstellung leichter und dennoch stabiler Teile. Für ästhetische Funktionen sind auch Holzfasern, Keramikpartikel und Pflanzenfasern in Kombination mit PLA zu finden. Wie bereits erwähnt, gibt es verschiedene Arten von Verstärkungen: Kurz-, Lang- oder Endlosfasern. Im ersten Fall werden Kurzfasern, die aus Segmenten von weniger als einem Millimeter Länge bestehen, mit herkömmlichen Thermoplasten vermischt, um die Steifigkeit und Festigkeit der Bauteile zu erhöhen.
Die beste Leistung ergibt sich aus der kontinuierlichen Faserverstärkung. Die Herstellung von Teilen aus Endlosfaserverbundwerkstoffen ist nicht so einfach wie die Herstellung von Kurzfaserverbundwerkstoffen, da die Fasern beim Extrudieren des Thermoplasts kontinuierlich in den Thermoplasten integriert werden müssen. Fasern können auch nach Designtechniken verlegt werden, die das Gewichts-Festigkeits-Verhältnis und den Materialverbrauch eines Teils optimieren, auch bekannt als DfAM-Techniken (Design for Additive Manufacturing). Dank der Endlosfaserverstärkung ist es möglich, Teile so widerstandsfähig wie Metall herzustellen.
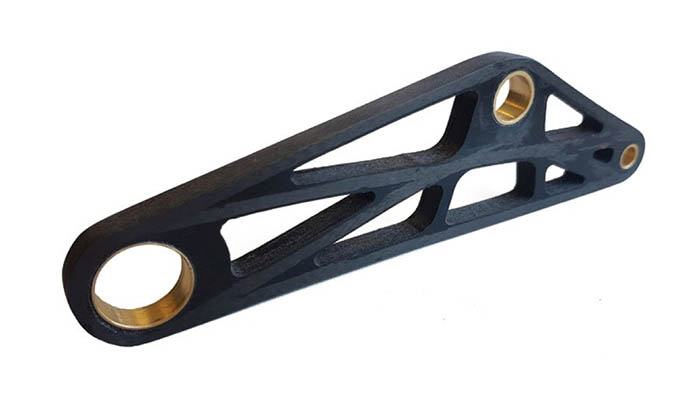
Ein 3D-gedrucktes Teil mit Kohlefaserverstärkung, mit einem höheren Verhältnis von Festigkeit zu Gewicht und geringerem Materialverbrauch
3D-Drucktechnologien mit Verbundwerkstoffen
In der additiven Fertigung liegen Verbundwerkstoffe überwiegend in Form von Filamenten vor und werden daher vor allem in der Fertigung eingesetzt FDM-Druck. Aber auch Ansätze für Metallverbunde im Laserverfahren, wie etwa LPBF, sind auf dem Vormarsch. Beispielsweise hat Fraunhofer ein Verfahren zum Einsatz des Laserauftragschweißens (LMD) bei Metallverbundwerkstoffen entwickelt. Dies unterstreicht den Trend, dass die additive Fertigung von Verbundwerkstoffen auf dem Markt an Bedeutung gewinnt, und es wird erwartet, dass andere Technologien in Zukunft den 3D-Druck von Verbundwerkstoffen ermöglichen werden.
Im Wesentlichen unterscheiden sich die 3D-Drucktechnologien für Verbundwerkstoffe je nach Art des verwendeten Verbundwerkstoffs. Kurzfaserverbundwerkstoffe können mit dem normalen FDM-Verfahren extrudiert werden, da das Filament bereits die Faser enthält. Darüber hinaus kann die Druckqualität durch die Menge der zerkleinerten Fasern in der Matrix beeinträchtigt werden. Kurzfaserverbundstoffe verstärken das gesamte Stück gleichmäßig. Ab einem bestimmten Schwellenwert verliert das 3D-gedruckte Teil jedoch an Oberflächenqualität. Andererseits ist der 3D-Druck mit Endlosfasern ein komplizierterer Prozess, bei dem zwei Düsen gleichzeitig gedruckt werden müssen. Typischerweise extrudiert eine Düse Thermoplast und die andere Faser. Ein Drucker, der dies ermöglicht, ist der Markforged Mark Two. Letzterer fügt im FDM-Verfahren langfaserige Materialien in die von ihm hergestellten Teile ein. Auf diese Weise werden die Teile nur dort verstärkt, wo es tatsächlich notwendig und gewünscht ist.
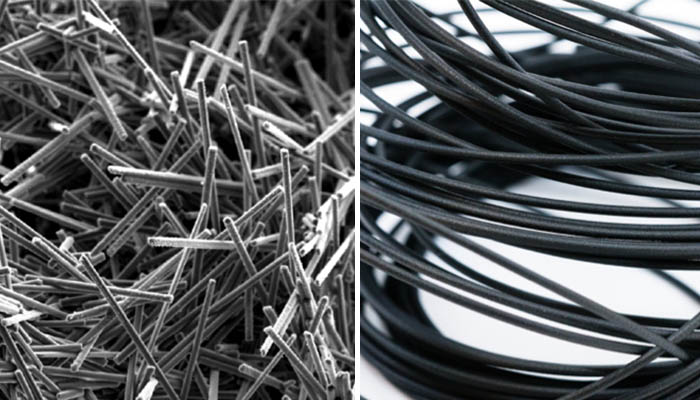
Links sieht man die kurzen Fasern, die aus Segmenten von weniger als einem Millimeter Länge bestehen. Rechts das mit kurzen Fasern verstärkte Filament.
Beim FDM-3D-Druck mit Verbundwerkstoffen wird häufig eine Düse mit größerem Durchmesser benötigt. Normalerweise gibt der Hersteller vor, welche Einstellung vorgenommen werden muss. Bei Glasfaser sollte die Düse auf einen Durchmesser von mindestens 0,6 mm eingestellt werden, bei Kohlefaser auf 0,4 mm und bei Kevlar beginnt man mit 0,6 mm und verringert sich dann schrittweise auf 0,4 mm. Wenn der Verbund Holzpartikel enthält, sollten Sie den Durchmesser zwischen 0,6 mm und 0,8 mm einstellen.
Darüber hinaus ist zu beachten, dass Verbundfilamente zu einem erhöhten Verschleiß an Hotend, Rohren und Extruderkomponenten führen können. Um dies zu vermeiden, empfehlen wir die Verwendung gehärteter Düsen, insbesondere für Carbon-, Glas- und Kevlar-Filamente. Außerdem ist es wichtig, die Spule während des Druckens richtig zu positionieren, um den Weg zum Extruder zu optimieren, damit er nicht zu lang wird. Zusätzlich zu diesen Vorsichtsmaßnahmen ist es aufgrund der höheren Viskosität von Verbundfilamenten erforderlich, die Druckgeschwindigkeit zu reduzieren und nicht die Geschwindigkeit des Basismaterials zu nutzen. Dennoch bieten Verbundwerkstoffe den Vorteil, dass sie beim Abkühlen nahezu keine Schrumpfung aufweisen und daher weniger anfällig für Druckfehler wie Verzug sind.
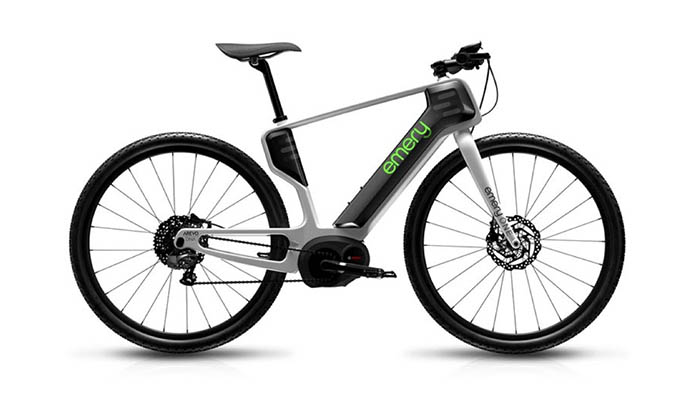
Der Fahrradrahmen von AREVO wurde im Endlosfaser-3D-Druck hergestellt | Bildnachweis: AREVO
Anwendungen von Verbundwerkstoffen
Mit verstärkenden Materialien drucken zu können, war das Ziel zahlreicher Startups in der 3D-Druckbranche. In den letzten Jahren haben wir festgestellt, dass immer mehr Maschinen und Technologien auf den Markt gebracht werden, um neue Anwendungen zu ermöglichen, insbesondere in Industriebereichen wie der Luft- und Raumfahrt und der Automobilindustrie. Wie bereits erwähnt, ist Kohlefaser eines der am häufigsten verwendeten Verbundmaterialien im 3D-Druck, insbesondere für anspruchsvolle Anwendungen wie funktionale Prototypen, Automobilteile und starke und dennoch leichte Komponenten. Dadurch erfreuen sich Kohlefaserverbundwerkstoffe auch im Sportbereich immer größerer Beliebtheit. Spitzensportler nutzen Carbon, um leichtere und damit schnellere Fahrräder herzustellen. Diese Vorteile werden auch in der Formel 1, im Automobilbereich und sogar in Sportarten wie Tennis und Rudern genutzt.
Der Markt für Verbundwerkstoffe wächst und neue Materialkombinationen werden neue Anwendungen ermöglichen. Engineering Materials erforscht den Einsatz additiver Verstärkungskomponenten. In China haben Forscher die Vorteile der Zugabe von Kohlenstofffasern zu Hochleistungsthermoplasten wie PEEK untersucht, während Sandvik 2019 den ersten Diamantverbundwerkstoff entwickelte. Normalerweise ist die Verwendung von Diamant in der additiven Fertigung nicht möglich, da er zu hart ist. Durch die Herstellung eines Diamantverbundwerkstoffs können die Materialeigenschaften jedoch für viele harte Werkzeuge (Bergbau, Bohren oder Zerspanen) und sogar für medizinische Implantate genutzt werden!
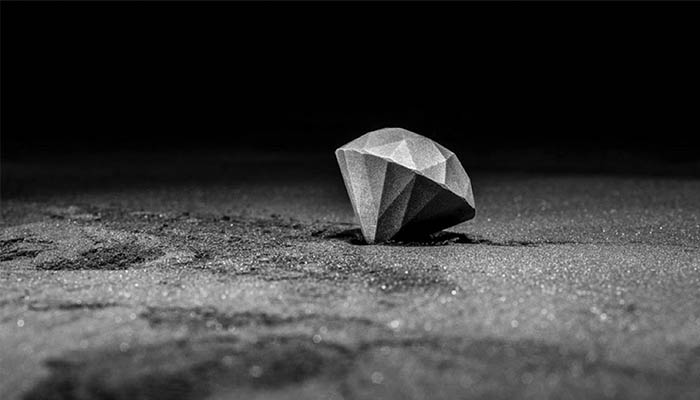
Der von Sandvik geschaffene Verbunddiamant
Hersteller von Verbundfilamenten und 3D-Druckern
Offensichtlich sind Verbundwerkstoffe tendenziell teurer als Standardwerkstoffe. Allerdings variieren die Preise je nach Hersteller und verwendetem Verbundwerkstoff. Der Preis einer Rolle variiert zwischen 150 und 500 Euro. Auch ein Verbundwerkstoff erfordert für seinen Einsatz einen Drucker mit besonderen Eigenschaften. Diese Drucker verfügen oft über eine eigene Technologie, die von den Herstellern unterschiedlich beschrieben und vermarktet wird. Markforged beispielsweise hat die CFF-Technologie (Continuous Carbon Fiber) für die von ihm angebotenen Verbunddrucker entwickelt. Anisoprint nannte es CFC (Continuous Fiber Coextrusion). Ein bekannter Name, der die Liste der Verbunddrucker ergänzt, ist Stratasys. Mit den 3D-Druckern F190 CR und F370 CR hat Stratasys die F123-Serie erweitert, um Drucker anzubieten, die mit Verbundwerkstoffen, insbesondere solchen mit hoher Steifigkeit und Festigkeit, kompatibel sind.
Eine weitere interessante Technologie ist die von AREVO patentierte. Es basiert auf der gerichteten Energieabgabetechnik, bei der ein Laser das Filament und die Kohlefaser gleichzeitig erhitzt, während eine Walze sie zusammenpresst. Das Schweizer Unternehmen 9T Labs hat beispielsweise ein ergänzendes System für reguläre 3D-Drucker entwickelt, das den 3D-Druck von Verbundwerkstoffen ermöglicht. Dieses 3D-Druckverfahren nennt sich AFT (Additive Fusion Technology). Schließlich nutzt Continuous Composites eine Hybridtechnologie, bei der das Fasergarn mit Harz imprägniert und anschließend mit UV-Licht ausgehärtet wird, ähnlich wie beim SLA-3D-Druck.
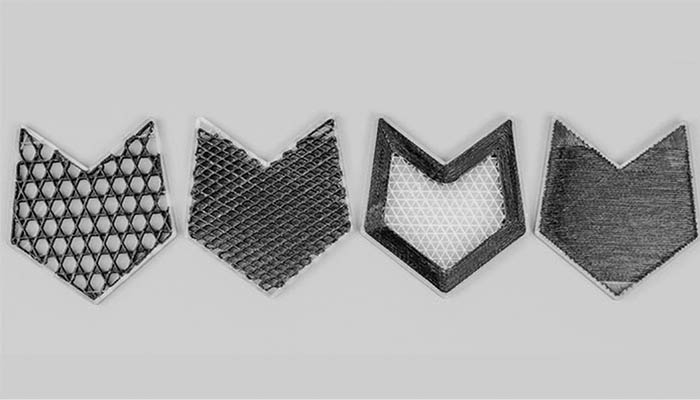
Die Software von Anisoprint kann mehrere Arten von endlosfaserverstärkten Füllungen erzeugen
Auch unter den Herstellern von Verbundfilamenten finden sich namhafte Namen. Markforged bietet Glasfaser- und Kevlar-Verbundwerkstoffe an. Owens Corning ist auch für seine glasfaserverstärkten Materialien bekannt. Auch Formfutura, BASF und XYZPrinting haben Verbundfilamente in ihr Sortiment aufgenommen. Unter den Kurzfaserverbundwerkstoffen stechen die Filamenthersteller Roboze, 3DXTech und ColorFabb hervor.