
Guida ai materiali per la stampa 3D: i compositi
Fonte: 3dnatives.com
I materiali compositi nascono dall’unione di almeno due materiali diversi. Uno funge da matrice e ha lo scopo di conservare la struttura, mentre l’altro fornisce proprietà aggiuntive come materiale di rinforzo. L’obiettivo di un materiale composito è aggiungere proprietà aggiuntive al materiale madre e, se necessario, neutralizzare le sue proprietà critiche. Aggiungendo le proprietà del rispettivo materiale di rinforzo al materiale madre, quest’ultimo ottiene migliori proprietà meccaniche, un colore diverso, ritardabilità alla fiamma, stabilità, capacità di carico, ecc. I materiali compositi si distinguono globalmente per le loro caratteristiche materiali (metalliche, minerali, ceramiche, organiche) o per la loro geometria. In base alle proprietà geometriche, si distinguono in:
- Compositi particellari
- Compositi in fibre (corte, lunghe o continue)
- Compositi stratificati e strutturati
I compositi in fibra sono particolarmente diffusi. Probabilmente la più diffusa sul mercato è la fibra di carbonio, seguita dalla fibra di vetro, che è un’altra delle più utilizzate nella produzione additiva.
Proprietà dei materiali compositi nella stampa 3D
I materiali rinforzati per la produzione additiva sono spesso a base di nylon, ma anche di ABS, PLA, PC e PETG. Attualmente, i compositi più utilizzati nella stampa 3D sono la fibra di carbonio, la fibra di vetro e la fibra aramidica Kevlar (PPD-T). Questi materiali offrono vantaggi per la realizzazione di parti leggere ma resistenti. Per le funzioni estetiche, si possono trovare anche fibre di legno, particelle di ceramica e fibre vegetali in combinazione con il PLA. Come già detto, esistono diversi tipi di rinforzi: fibre corte, lunghe o continue. Nel primo caso, le fibre corte, costituite da segmenti di lunghezza inferiore a un millimetro, vengono mescolate ai termoplastici convenzionali per aumentare la rigidità e la resistenza dei componenti.
Le migliori prestazioni derivano dal rinforzo con fibre continue. Il processo di creazione di parti con compositi di fibre continue non è semplice come quello con compositi di fibre corte perché le fibre devono essere integrate nella termoplastica in maniera continua man mano che la termoplastica viene estrusa. Le fibre possono anche essere posate secondo tecniche di design che ottimizzano il rapporto peso-resistenza di un pezzo e il consumo di materiale, anche note come tecniche DfAM (Design for Additive Manufacturing). Grazie al rinforzo con fibre continue è possibile creare parti resistenti come il metallo.
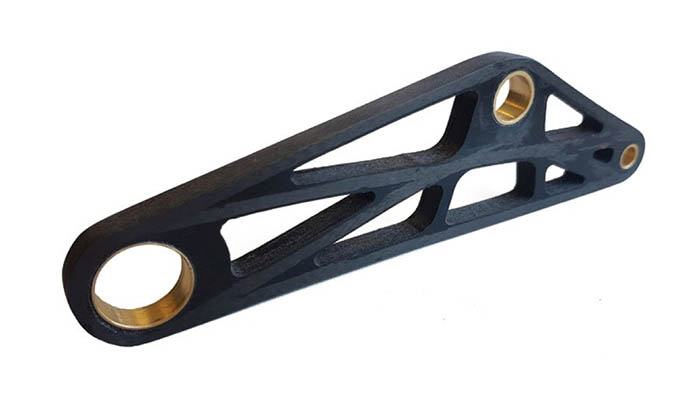
Un pezzo stampato in 3D impiegando un rinforzo di fibre di carbonio, con un maggiore rapporto peso-resistenza e un minore consumo di materiale
Tecnologie di stampa 3D che utilizzano compositi
Nella produzione additiva, i materiali compositi sono principalmente sotto forma di filamenti e vengono quindi utilizzati principalmente nella stampa FDM. Tuttavia, si stanno facendo strada anche approcci per i compositi metallici nel processo laser, come l’LPBF. Ad esempio, Fraunhofer ha sviluppato un processo per utilizzare la saldatura a riporto laser (LMD) con i compositi metallici. Ciò sottolinea la tendenza della produzione additiva dei compositi a guadagnare terreno sul mercato e si prevede che in futuro altre tecnologie consentiranno la stampa 3D dei compositi.
Essenzialmente, le tecnologie di stampa 3D dei compositi si differenziano a seconda del tipo di composito utilizzato. I compositi a fibra corta possono essere estrusi con il normale processo FDM, poiché il filamento contiene già la fibra. Inoltre, la qualità di stampa può essere influenzata dalla quantità di fibre triturate nella matrice. I compositi a fibra corta rinforzano uniformemente l’intero pezzo. Oltre una certa soglia, tuttavia, la parte stampata in 3D perde qualità superficiale. D’altra parte, la stampa 3D a fibra continua è un processo più complicato che richiede due ugelli per stampare contemporaneamente. Di solito, un ugello estrude la termoplastica e l’altro la fibra. Una stampante che lo rende possibile è la Markforged Mark Two. Quest’ultima inserisce i materiali a fibra lunga nelle parti che crea con il processo FDM. In questo modo, i pezzi vengono rinforzati solo dove è effettivamente necessario e desiderato.
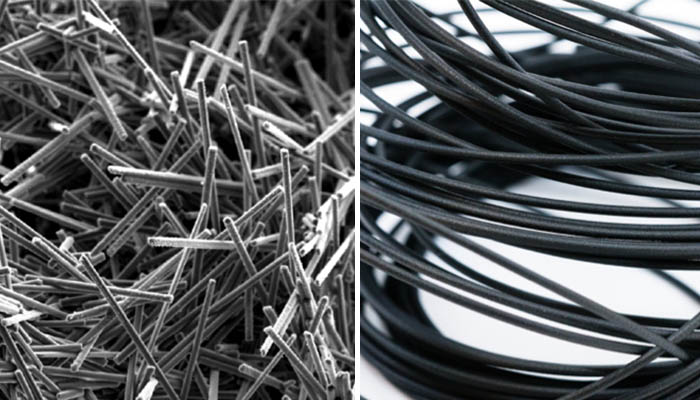
A sinistra puoi vedere le fibre corte, composte da segmenti di lunghezza inferiore a un millimetro. A destra, il filamento rinforzato con fibre corte.
Nella stampa 3D FDM con materiali compositi, spesso è necessario un ugello di diametro maggiore. Normalmente il produttore specifica quale impostazione deve essere effettuata. Per la fibra di vetro, l’ugello deve essere impostato su un diametro di almeno 0,6 mm, per la fibra di carbonio su 0,4 mm e per il kevlar si inizia con 0,6 mm e poi si scende gradualmente a 0,4 mm. Se il composito presenta particelle di legno, è necessario impostare il diametro tra 0,6 mm e 0,8 mm.
Inoltre, va notato che i filamenti compositi possono causare una maggiore usura dell’hotend, dei tubi e dei componenti dell’estrusore. Per evitare ciò, si consiglia di utilizzare ugelli temprati, soprattutto per i filamenti di carbonio, vetro e kevlar. È inoltre importante posizionare correttamente la bobina durante la stampa per ottimizzare il percorso verso l’estrusore in modo che non sia troppo lungo. Oltre a queste precauzioni, a causa della maggiore viscosità dei filamenti compositi, è necessario ridurre la velocità di stampa e non utilizzare la velocità del materiale di base. Ciononostante, i materiali compositi offrono il vantaggio di non ritirarsi quasi per niente quando si raffreddano e quindi hanno meno probabilità di causare errori di stampa come la deformazione.
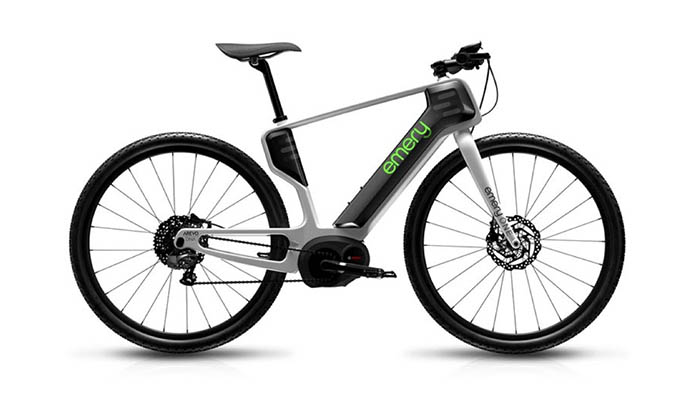
Il telaio per bici di AREVO è stato creato utilizzando la stampa 3D a fibra continua | Crediti: AREVO
Applicazioni dei materiali composti
Essere in grado di stampare con materiali di rinforzo è stato l’obiettivo di numerose startup nel settore della stampa 3D. Negli ultimi anni abbiamo notato il lancio sul mercato di un crescente numero di macchine e tecnologie per abilitare nuove applicazioni, soprattutto in settori industriali come quello aerospaziale e automobilistico. Come già accennato, la fibra di carbonio è uno dei materiali compositi più utilizzati nella stampa 3D, soprattutto per applicazioni impegnative come prototipi funzionali, parti di automobili e componenti resistenti ma leggeri. Di conseguenza, i compositi in fibra di carbonio stanno diventando sempre più popolari anche nel settore sportivo. Gli atleti d’élite utilizzano il carbonio per creare biciclette più leggere e quindi più veloci. Questi vantaggi vengono sfruttati anche in Formula 1, nel settore automobilistico e persino in sport come il tennis e il canottaggio.
Il mercato dei materiali compositi è in crescita e nuove combinazioni di materiali consentiranno nuove applicazioni. I materiali ingegneristici stanno esplorando l’uso di componenti di rinforzo additivi. In Cina, i ricercatori hanno studiato i vantaggi dell’aggiunta di fibre di carbonio a materiali termoplastici ad alte prestazioni come il PEEK, mentre Sandvik ha creato il primo composito di diamante nel 2019. Normalmente non è possibile utilizzare il diamante nella produzione additiva perché è troppo duro. Tuttavia, creando un composito di diamante, le proprietà del materiale possono essere utilizzate per molti strumenti duri (estrazione, foratura o lavorazione) e anche per impianti medici!
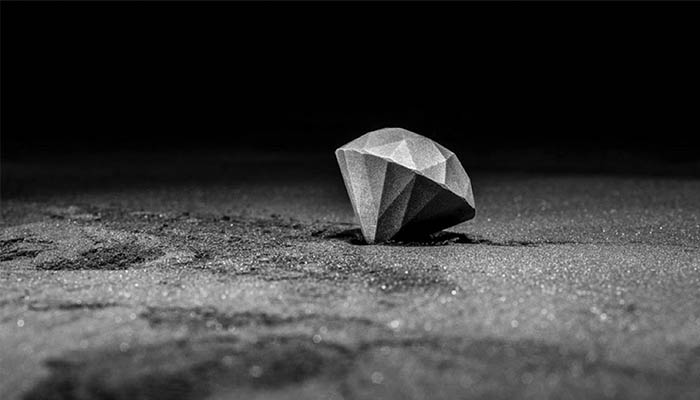
Il diamante composito creato da Sandvik
Produttori di filamenti compositi e stampanti 3D
Ovviamente, i materiali compositi sono tendenzialmente più costosi dei materiali standard. Tuttavia, i prezzi variano a seconda del produttore e del composito utilizzato. Il prezzo di una bobina varia da 150 a 500 euro. Un materiale composito richiede anche una stampante con proprietà speciali per il suo utilizzo. Tali stampanti sono spesso dotate di una tecnologia propria, descritta e commercializzata in modo diverso dai produttori. Markforged, ad esempio, ha sviluppato la tecnologia CFF (Continuous Carbon Fiber) per le stampanti di compositi che offre. Anisoprint l’ha chiamata CFC (Continuous Fiber Coextrusion). Un nome noto che si aggiunge all’elenco delle stampanti per compositi è Stratasys. Con le stampanti 3D F190 CR e F370 CR, Stratasys ha ampliato la serie F123 per offrire stampanti compatibili con i materiali compositi, in particolare quelli ad alta rigidità e resistenza.
Un’altra tecnologia interessante è quella brevettata da AREVO. Si basa sulla tecnica di erogazione direzionale dell’energia, che utilizza un laser per riscaldare simultaneamente il filamento e la fibra di carbonio mentre un rullo li pressa insieme. La società svizzera 9T Labs, ad esempio, ha sviluppato un sistema complementare per le normali stampanti 3D che consente la stampa 3D di materiali compositi. Questo processo di stampa 3D viene chiamato AFT (Additive Fusion Technology). Infine, Continuous Composites utilizza una tecnologia ibrida in cui il filato di fibra è impregnato di resina e poi polimerizzato con luce UV, simile alla stampa 3D SLA.
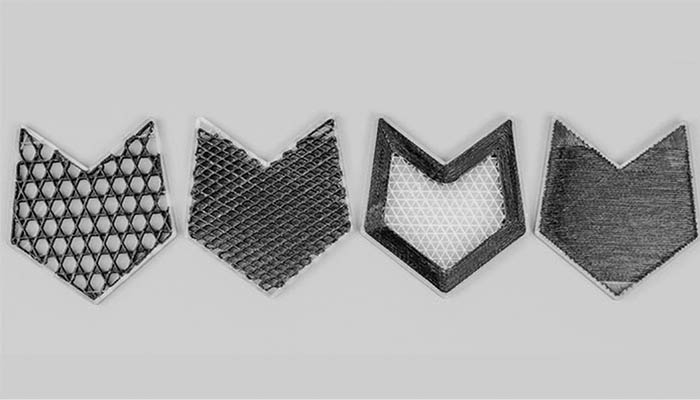
Il software di Anisoprint può generare riversi tipi di riempimenti rinforzati con fibre continue
Tra i produttori di filamenti compositi si trovano anche nomi noti. Markforged offre compositi in fibra di vetro e Kevlar. Anche Owens Corning è nota per i suoi materiali rinforzati con fibre di vetro. Anche Formfutura, BASF e XYZPrinting hanno aggiunto filamenti compositi alla loro gamma. Tra i compositi in fibra corta, spiccano i produttori di filamenti Roboze, 3DXTech e ColorFabb.