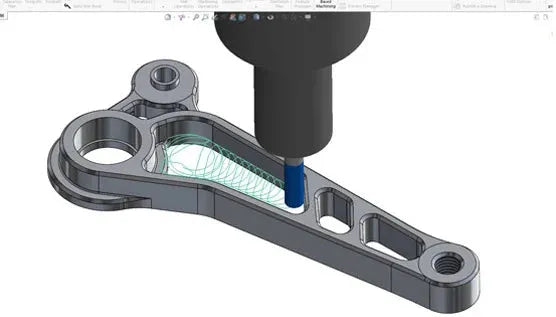
3D Printing Software
Source: 3dnatives.com
At the heart of every 3D printed piece is a digital model, created or modified in 3D modeling software. When we talk about 3D modeling software, we most often mean CAD software, but we can also refer to optimization and simulation software or slicing and repair software. STL file. In addition, there are also software on the market for managing production flows, which have nothing to do with modeling, but which are increasingly useful for companies that want to industrialize their production. In fact, the 3D printing software sector is rich, which is why we will divide it for you below!
In terms of modeling, it is important to remember that when working on a 3D model, there are many parameters to consider. It is therefore important to plan in advance complex geometries, mechanical characteristics, weight, cost, 3D printing supports, etc. In this guide, we analyze the different types of 3D printing software on the market.
3D modeling software
When it comes to modeling a piece, the user has several options: solid, surface, or organic modeling. The final choice of software will be made based on the needs and the rendering that you want to give to the 3D printed object. This can also be influenced by the 3D printing technology or even the desired material.
Solid modeling
For solid modeling, CAD software is often the most suitable solution. There is a wide choice of software for this category. When choosing which CAD software to use for modeling, you should first be guided by your level of experience. If you are a beginner, choose a simpler solution, because modeling can be complex at first. Your choice will also depend on some of the features you may need, usually dictated by the industry you work in. Finally, ask yourself whether you want a cloud solution or not.
CAD software often uses parametric design which, as the name suggests, allows a 3D model to be defined by easily replaceable parameters: modeling takes shape through programming, rather than drawing.
This type of solution allows the user to change the characteristics of a piece (length, angle, coordinates relative to a reference point or distance). It all starts with a drawing composed of closed 2D curves; then the user adds a series of functions to create a 3D shape.
This technique is similar to generative design, which makes it possible to define design goals and constraints and analyze the performance of each parameter (material, weight, strength, cost, etc.). The software explores all possible permutations of a design, quickly generating alternative designs, testing and learning at each iteration what works and what doesn't.
Parametric design is more rigid than direct modeling and is mainly used by mechanical engineers and industrial designers. Some of the most popular software with such features are Solidworks, Catia, CREO, Fusion 360 and FreeCAD for the free version.
It should be noted that, according to a survey conducted by 3DHubs among 750 professionals, Solidworks is the most used CAD software, by engineers (50%) and designers (49%). It is followed by AutoCAD, Fusion 360 and Rhino solutions, aimed at designers.
- Parametric Design with SOLIDWORKS
- Generative design with Autodesk
- FreeCAD 3D modeling software
Surface modeling
This type of design is usually appreciated by users who are looking for aesthetics. As the name suggests, surface modeling software defines the surface of the object and not its interior. In most cases, it is used in the artistic sector, especially in 3D animation. The best-known solutions are CATIA by Dassault Systèmes, Blender or Rhinoceros. The latter, for example, is a tool particularly appreciated by industrial designers and architects.
Organic modeling
It allows you to create free-form surfaces with extremely complex details and is usually used to draw characters or sculptures. The two most used software on the market are undoubtedly ZBrush by Pixologic and Mudbox by Autodesk. The latter are extremely renowned in the film industry and among jewelry designers.
Once you have created your 3D model in a modeling software, the next step is to make sure it is 3D printable. There are many solutions to optimize or even simulate the printing of the part, thus reducing the risk of printing errors.
- ZBrush is one of the most popular software
- Mudbox Software
- Organic modeling software allows to achieve a high level of precision
Simulation and optimization software
Topological optimization software cannot go unmentioned when it comes to modeling and simulation. This tool makes it possible to define the best distribution of material in a given volume subject to limits. In other words, it removes material from a part when it is not necessary for its correct functioning. Topological optimization allows to respect the load and resistance limits, considerably reducing the final weight. These optimization software offer more complex geometries, weight savings and, consequently, better performance in sectors such as automotive or aeronautics. Among the existing solutions, we can mention solidThinking Inspire, Ansys or 4D_Additive, or Crea Simulate.
The simulation software instead allows you to digitally predict the results of a 3D printing process. They give the user precious time as they identify possible printing errors in a few minutes, thus reducing the costs associated with printing waste. The user can simulate various parameters: distortion, temperature or post-processing. It also makes it possible to evaluate the need for printing supports and identify critical areas where deformations can occur.
The parameters to be simulated depend on the printing technology used. For example, for the Fused Deposition Modeling (FDM), the focus will be on assessing the risk of warping; in these cases, simulation will help determine whether the part needs to be redesigned or whether adhesion to the plate needs to be increased, for example.
If the Selective Laser Sintering (SLS), you may see hot or cold spots forming on your part, causing the part to warp or have poor surface quality. By simulating the thermal properties of your 3D model, these errors can be avoided at print time.
- Topology optimization tools allow you to optimize material consumption
- Siemens Simulation Tool
- EOS software allows you to visualize thermal zones
STL File Slicer and Repair Software
The slicers
It's a must when you want to 3D print: the slicer, or slicing software, cuts the 3D model into thin digital layers that correspond to the layers of material extruded by the 3D printer.
The slicer transmits to the printer all the instructions it has to follow; these are usually written in a language called G-code. For example, the slicer defines the resolution, the printing speed or the height of the layer. It is therefore a central software in the process of additive manufacturing. For the FDM 3D printers There are two categories of slicers: open source universal software, such as Cura (developed by Ultimaker), Repetier and Slic3r or paid software such as Simplify3D, but also proprietary software such as ReplicatorG by MakerBot, ZSuite by Zortrax or Voxelizer by ZMorph.
Repair
While simulation software catches errors before printing, STL repair software can fix them, which is a key asset in the printing process. Some slicers can catch basic defects that exist at the 3D file level, but they don’t necessarily catch everything.
Fortunately, there is dedicated software available to repair damaged STL files, ensuring an optimal 3D printing process. Some tools are downloadable, others are available online, open-source or otherwise. Whatever your level, you should be able to find a solution that works for you. Some of the most popular are NetFabb and MakePrintable.
3D Print Management Tools
If you need to run multiple 3D prints at the same time in different locations or if your company has a large inventory of machines, there are 3D printer management solutions available to streamline your workflow. These typically include remote monitoring, multi-user management, optimized production bin filling, or improved machine control, all to simplify the user experience and automate production steps.
Some of the software currently available are Octoprint, Astroprint or PrintRun. 3D Printer OS, for example, connects the different 3D printers present in a network to coordinate all the printing and increase productivity. For manufacturers, software publishers such as Dassault Systèmes, Siemens, 3YOURMIND and AMFG have also launched solutions for this need of the industry.
- Astroprint Helps Your 3D Printing Workflow
- 3D Printer OS
- The 3YOURMIND platform
Other 3D printing software
As you may have understood, when it comes to 3D printing software there are numerous tools. To complete this overview, we present you with 2 other types of solutions:
– Software to protect your designs: There are some solutions on the market designed to protect your data and allow repeatability and traceability of production. When a user models a piece, it can be very important to protect some data, more or less sensitive, and ensure that digital flows are encrypted. Some software programs now allow you to secure the entire line, from CAD to production. This is the case, for example, of Identify3D.
– 3D scanning applications: One modeling option is 3D scanning. The user can directly create a 3D file from a scanned object. There are many scanners available today, but they can sometimes be complicated to use or quite inaccessible. 3D scanning applications are a good alternative. Some are downloadable on smartphones and allow you to scan directly from a phone's camera. In particular, we are referring to photogrammetry software which, as the name suggests, uses photographs to recreate a digital model. If you want to know more, you can take a look at our ranking of the best photogrammetry software present on the market.