
3D Printing Materials Guide: Metals
Source: 3dnatives.com
Metal 3D printing is one of the fastest growing advanced manufacturing technologies in the industry. In fact, according to a report published by Grand View Research, the global market for this process was valued at $6.36 billion in 2022. Furthermore, the sector is set to register a compound annual growth rate (CAGR) of 24.2% between now and 2030. This increase is due, in part, to the wide variety of materials compatible with this technology. Whether it is 3D printers which use systems of powder bed fusion, DED, EBM or even metal extrusion, the possibilities of these materials are virtually limitless. In this comprehensive guide, we present the most commonly used metals in 3D printing and the characteristics of each.
Aluminum
This material offers an excellent compromise between lightness and strength. In addition to being resistant to corrosion, it can also be welded. Compared to steel, it is less resistant and more sensitive to high temperatures. It is mainly used in areas where weight is crucial, such as in the mechanical parts of racing cars, aeronautics, aerospace, bicycles, etc. It is rarely present in its pure state and is more frequently found in the form of alloys with metals that improve its physical and mechanical properties, such as silicone and magnesium. A typical example is the aluminum AISi10Mg, sold in powder form by the German manufacturer EOS. This makes it possible to produce solid and complex parts.
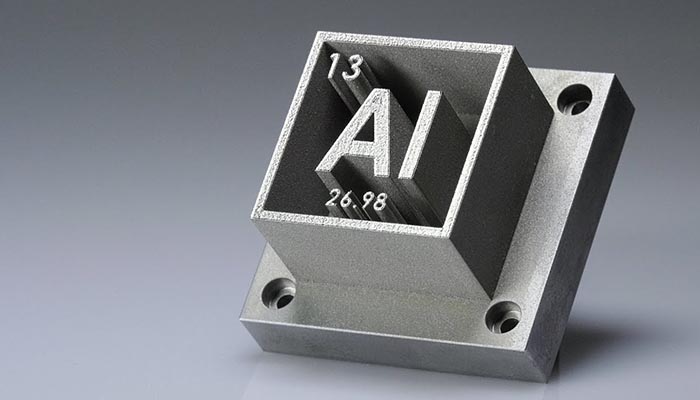
Aluminum alloys
As previously mentioned, aluminum alloys are more common in pure form and are traditionally used in many industrial applications. In addition, they have a high strength-to-weight ratio, in fact they show good resistance to stress and metal corrosion.
Steel
As one of the most common metals in the industry for the production of spare parts, it is not surprising that steel was the first metal used in 3D printing. Within this group, we can find two types: stainless steel and maragin tool steel. Stainless steel is widely used in everyday life, mechanical engineering and medicine. It has good metallic properties and produces a shiny and glossy surface. Several manufacturers in the 3D industry offer this material, including EOS, ProMetal and Desktop Metal. Some of its properties include: hardness, tensile strength, formability and impact resistance. It is also possible to print bronze or gold parts using stainless steel as a base material. This is achieved, for example, by coating the stainless steel powder layers with bronze injection glue during printing. On the other hand, EOS has developed the maragin MS1 steel, which is used in the production of tools and molds, due to its strength and fracture resistance.
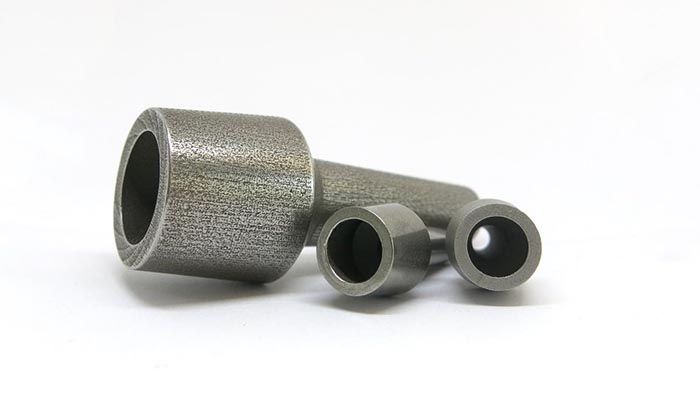
3D printed part in stainless steel.
Copper alloys
Copper is another metal used in additive manufacturing. Its properties include high electrical and thermal conductivity, ductility (plastic deformation without breaking) and malleability (deformation under compression). Copper is available in both filament and powder form for 3D printing. Its characteristics make this metal ideal for thermal management and electrical engineering applications (inductors, electrodes, heat exchangers, etc.), as well as for the construction of tools and fixtures. Some of its most common alloys are: CuNi2SiCr, CuCrZr, CuCP, Cu.
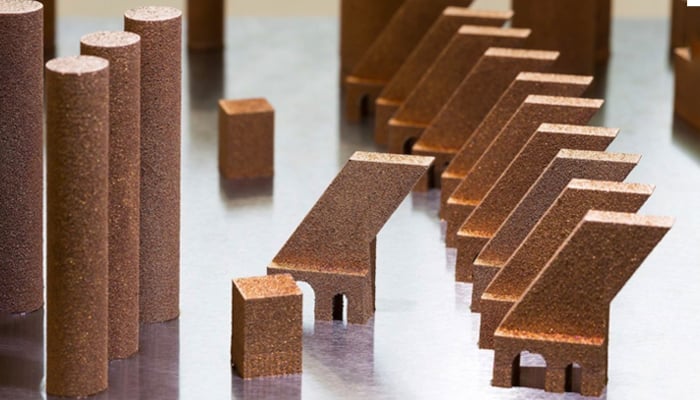
Gallium
Gallium is used as an alloy, with 25% indium. What makes this alloy special is that not only can it be melted at a low temperature of 29.7°C (85.46°F), but the two metals solidify on contact with air while the interior remains liquid, making it easy to print. Price remains the main barrier to using this material.
Titanium
Titanium is the flagship of the medical and aerospace industries, thanks to its excellent combination of strength and weight, biocompatibility and high resistance to corrosion. All titanium grades show extreme corrosion resistance, ductility and weldability, although grade one is slightly less workable than grades two, three and four. Grade four is the strongest. 3D printing makes it easier to produce titanium parts and avoids the impurities obtained with traditional techniques during the welding phase. However, a major disadvantage of this material is its high cost, as it is approximately 50 times higher than that of steel.
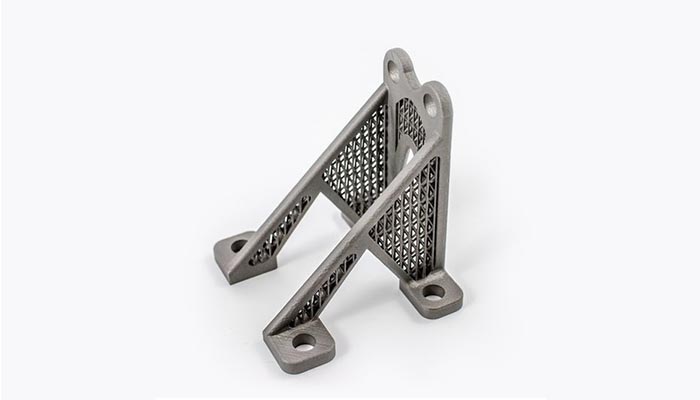
3D printed titanium piece.
Titanium alloys
Similar to aluminum alloys, titanium alloys have better mechanical and chemical properties. Ti6Al4V is the most widely used alloy, accounting for 56% of the total titanium market, due to its good balance of mechanical strength, ductility, fatigue resistance, and fracture toughness. These metals are used in additive manufacturing to produce a wide range of industrial components, including sheet metal, fasteners, rings, discs, and containers. Titanium alloys are also used to produce high-performance automotive engine parts, such as gearboxes and connecting rods.
Cobalt Chromium
Printed with technologies EBM and DMLS, cobalt alloys show better quality than those obtained using traditional manufacturing methods such as investment casting. Like titanium alloys, cobalt-chromium alloys such as CoCrMo are widely used in medicine for the production of prosthetics, both in orthopedics and dentistry (due to their rigidity, wear resistance and lack of corrosion). In addition, the automotive and aerospace industries use some highly heat-resistant cobalt-chromium-molybdenum alloys. EOS offers Cobalt-chromium MP1 and SP2 alloys that are resistant to high temperatures, up to 600°C (1,112°F). Arcam on the other hand markets ASTM F75, which is widely used for the production of tools and molds.
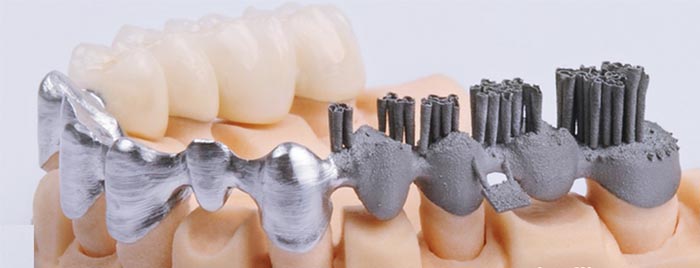
3D Printed Dental Implants
Nickel-based alloys
Nickel is an incredibly versatile material, available in powder or filament form and capable of being alloyed with other metals. Nickel-chromium superalloys, such as Inconel 718 and Inconel 625, produce strong, corrosion-resistant metal parts. These alloys are primarily used in industry aerospace, automotive, and petrochemical industries, where they are subjected to high stresses and temperatures. The mechanical properties of nickel-based alloys in additive manufacturing, such as Inconel 625, are significantly improved by the use of significant amounts of nickel, chromium, and molybdenum in the metal.
Precious metals
We have seen previously that it is possible to add glue to inject bronze and gold into a stamped steel object. Another way to stamp with these metals is metal casting. This is a lost wax mold, finished by hand. This method is widely used in jewelry and in the production of small objects. One of the problems and limitations of this casting method is that it must take into account the fine shapes to avoid, as well as ensuring a minimum thickness of 0.8 mm - 1 mm to ensure respect for the walls. The finishing stage is the key to obtaining a good surface finish, especially for silver pieces. Finally, with gold, it is possible to obtain different shades of color (pink, white and yellow).
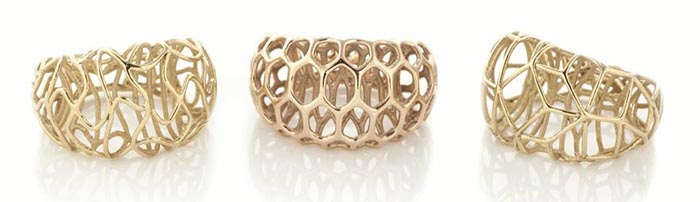
Finally, it is important to note that today it is possible to modify the atomic structure of the metal during 3D printing. This results in faster and more uniform solidification, which can lead to a stiffer and stronger metal.