
TPU for 3D Printing: Everything You Need to Know
Source: 3dnatives.com
Thermoplastic polyurethane (TPU) is an elastomer characterized by high flexibility and resistance, combining the properties of thermoplastics and rubbers. The flexibility of this polymer is due to the presence of alternating sequences of hard and soft segments in its chemical composition. In fact, by varying the proportion of these segments, the rigidity and flexibility of the material also change. This affects the transparency of the final pieces, the softness to the touch and the adhesion of the parts. In general, we can say that TPU is a polymer that guarantees the pieces various and extremely interesting properties. But what should we know before using TPU?
TPU Production and Characteristics
In terms of properties, it is important to know that this polymer has many advantages such as high resistance to impacts, wear, abrasion and cuts. In addition, it has a rather advanced layer adhesion that allows achieving excellent mechanical homogeneity at the level of the manufactured parts, making them isotropic. However, this type of material has some limitations that must be taken into account: TPU does not adapt well to hot environments, which is important since it does not resist high temperatures; in addition, the printing settings must vary depending on the technology used. Compared to TPE, another flexible filament, TPU is easier to print and maintains its elastic properties better at lower temperatures. The TPU material offers greater resistance to abrasion and oils and greases. Unlike more rigid thermoplastics, TPU filament has qualities such as flexibility and adaptability and does not present problems of deformation or delamination during the 3D printing process.
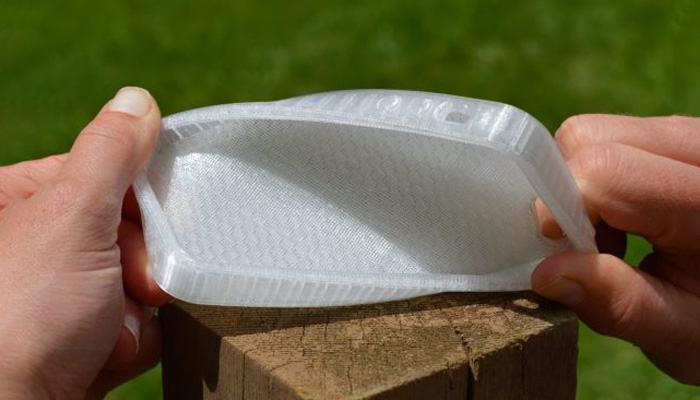
Thanks to its flexibility, TPU can be used to create cell phone cases.
TPU Filament Features in 3D Printing
When printing parts with TPU with technology FDM, we suggest applying a thin layer of glue to the print bed, which will help the material stick. It is also recommended that the extrusion nozzle reaches a temperature between 210 and 235 °C to melt the filament (although this depends on the manufacturer). These are general recommendations, but the success of TPU will depend on the setup of each 3D printer and proper calibration; therefore, it is recommended to do small tests with this material before starting on more complex prints.
For stereolithography, TPU is not recommended for small, thin models or those simulating high-elasticity materials. When setting up your model, it is recommended that models are in their final shape and oriented no more than 20° to the print bed. Thinner, taller parts will be more difficult to print, although additional supports can always be used to ensure an optimal result.
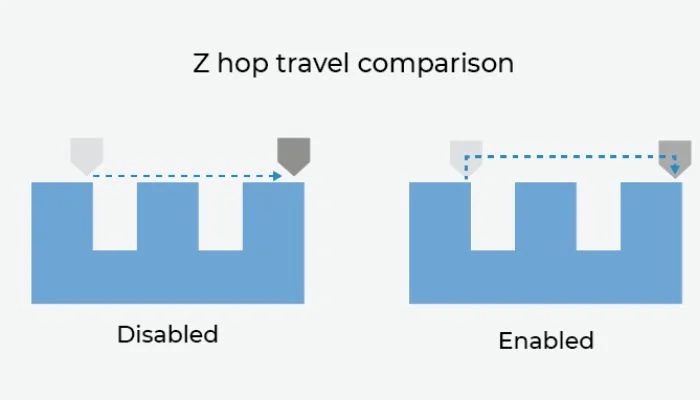
However, it is important to note that each machine and filament is different, so it is recommended to run tests to find the optimal retraction value. It is also important to note that this value can vary between different TPU filaments. TPU does not require a mandatory post-treatment, but there are some techniques that can be performed to improve its properties or aesthetic appearance. A common option is a polishing treatment to smooth the surface and remove layer marks, which can improve the final appearance of the printed object. A layer of paint or coating can also be applied to improve its resistance to water, dust and dirt.
Main applications
In the additive manufacturing industry, this material opens up a world of possibilities for different markets. To begin with, in footwear we find the creation of elastic soles and in the medical sector the creation of orthopedic models. On the other hand, in the aerospace sector, the development of instruments or sensors and in the automotive sector, the creation of tires and shock absorbers. We can also find TPU in the sports sector, in the production of protections for fitness equipment.
TPU is ideal for end-use parts, functional prototypes, concept models, and custom components. This type of material is widely used, for example, to make cell phone covers, as it protects the device from impacts and fractures.
Manufacturers and price of material
On the additive manufacturing market today we can find large companies that offer TPU to create flexible parts. Ultimaker has a filament called TUP 95A, which is compatible with its 3D printers Ultimaker S5, Ultimaker 3 and Ultimaker 2+ and with the latest printer released by the manufacturer, the UltiMaker S7. According to the company, the material supports up to 580% elongation at break; this filament is available in 4 different colors.
Another company is Formlabs, which last year introduced its “elastic resin” for SLA technology. This resin has a Shore hardness of 50A, as well as high elongation and energy return. The Shore value refers to the hardness of the material used, or in other words, how resistant a material is to dents. Lower values indicate lower resistance or softer materials. The elasticity and resistance of this material allows it to be used in multiple cycles. In addition, the technology allows for reduced costs and lead times by printing directly on soft parts.
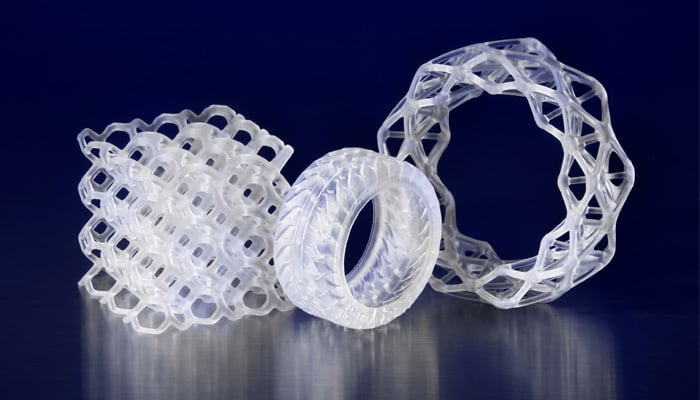
There are also other companies involved in the development of these materials such as Recreus, which offers a wide variety of 3D printing filaments. In particular, its renowned FilaFlex filament was born out of a need to innovate in 3D printing. Ignacio García, CEO of Recreus said: “ 3D printing technology itself was already innovative and this, added to the flexibility of the material to create flexible parts, such as shoes, demonstrated without a doubt the potential of additive manufacturing and FilaFlex ”. Other companies such as BASF offer the material in powder form. They have a line of TPU powders they call Ultrasint® and, for example, their TPU01 is designed specifically for HP’s Multi Jet Fusion 5200 series printers. The price of TPU filament is around 30-40 euros per kilogram.