
3D Printing Materials Guide: Composites
Source: 3dnatives.com
Composite materials are created by combining at least two different materials. One acts as a matrix and is intended to maintain the structure, while the other provides additional properties as a reinforcing material. The aim of a composite material is to add additional properties to the parent material and, if necessary, to neutralize its critical properties. By adding the properties of the respective reinforcing material to the parent material, the latter obtains better mechanical properties, a different color, flame retardancy, stability, load-bearing capacity, etc. Composite materials are generally distinguished by their material characteristics (metallic, mineral, ceramic, organic) or by their geometry. Based on the geometric properties, they are distinguished into:
- Particle Composites
- Fiber composites (short, long or continuous)
- Layered and structured composites
Fiber composites are particularly widespread. Probably the most widespread on the market is carbon fiber, followed by glass fiber, which is another of the most used in additive manufacturing.
Properties of composite materials in 3D printing
Reinforced materials for additive manufacturing are often nylon-based, but also ABS, PLA, PC, and PETG. Currently, the most widely used composites in 3D printing are carbon fiber, glass fiber, and Kevlar aramid fiber (PPD-T). These materials offer advantages for the production of lightweight but resistant parts. For aesthetic functions, wood fibers, ceramic particles, and plant fibers can also be found in combination with PLA. As mentioned, there are different types of reinforcements: short, long, or continuous fibers. In the first case, short fibers, consisting of segments less than a millimeter long, are mixed with conventional thermoplastics to increase the stiffness and strength of the components.
The best performance comes from continuous fiber reinforcement. The process of creating parts with continuous fiber composites is not as simple as with short fiber composites because the fibers must be integrated into the thermoplastic in a continuous manner as the thermoplastic is extruded. Fibers can also be laid out in design techniques that optimize a part’s strength-to-weight ratio and material consumption, also known as Design for Additive Manufacturing (DfAM) techniques. Continuous fiber reinforcement can create parts that are as strong as metal.
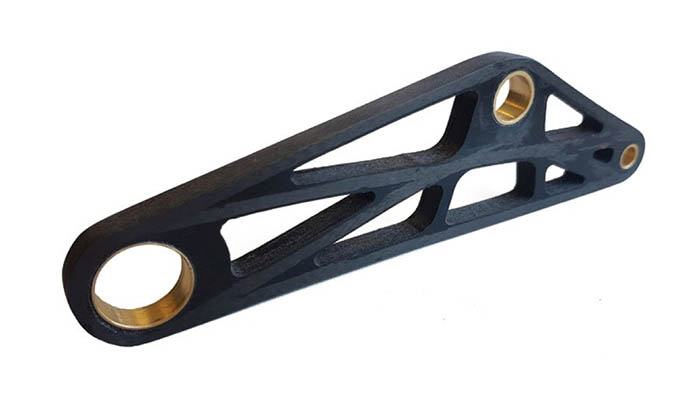
A 3D printed part using carbon fiber reinforcement, with a higher weight-to-strength ratio and lower material consumption
3D Printing Technologies Using Composites
In additive manufacturing, composite materials are mainly in the form of filaments and are therefore mainly used in FDM printing. However, approaches for metal composites in the laser process, such as LPBF, are also gaining ground. For example, Fraunhofer has developed a process for using laser deposition welding (LMD) with metal composites. This underscores the trend of additive manufacturing of composites gaining ground in the market, and it is expected that other technologies will enable 3D printing of composites in the future.
Essentially, composite 3D printing technologies differ depending on the type of composite used. Short-fiber composites can be extruded with the regular FDM process, since the filament already contains the fiber. Additionally, the print quality can be influenced by the amount of shredded fibers in the matrix. Short-fiber composites uniformly reinforce the entire part. Beyond a certain threshold, however, the 3D printed part loses surface quality. On the other hand, continuous-fiber 3D printing is a more complicated process that requires two nozzles to print at the same time. Typically, one nozzle extrudes the thermoplastic and the other the fiber. One printer that makes this possible is the Markforged Mark Two. It inserts long-fiber materials into the parts it creates with the FDM process. This way, the parts are only reinforced where it is actually needed and desired.
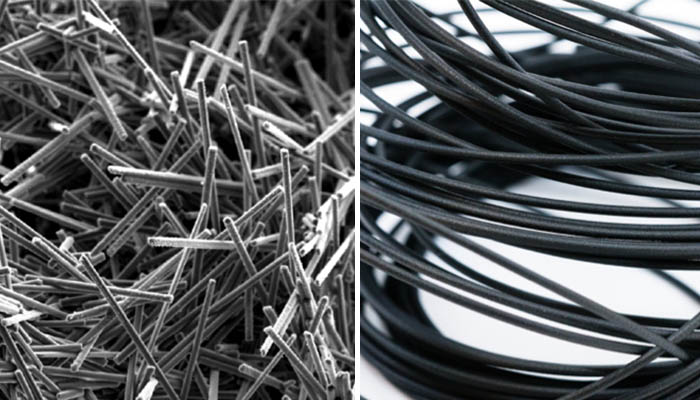
On the left you can see the short fibers, composed of segments less than a millimeter long. On the right, the short fiber reinforced filament.
When FDM 3D printing composites, a larger nozzle diameter is often required. The manufacturer usually specifies which setting should be made. For glass fiber, the nozzle should be set to a diameter of at least 0.6 mm, for carbon fiber to 0.4 mm, and for Kevlar you start with 0.6 mm and gradually decrease to 0.4 mm. If the composite has wood particles, you should set the diameter between 0.6 mm and 0.8 mm.
Additionally, it should be noted that composite filaments can cause increased wear on the hotend, tubing, and extruder components. To avoid this, it is recommended to use hardened nozzles, especially for carbon, glass, and kevlar filaments. It is also important to position the spool correctly during printing to optimize the path to the extruder so that it is not too long. In addition to these precautions, due to the higher viscosity of composite filaments, it is necessary to reduce the printing speed and not use the speed of the base material. However, composite materials offer the advantage of almost no shrinkage when cooling and are therefore less likely to cause printing errors such as warping.
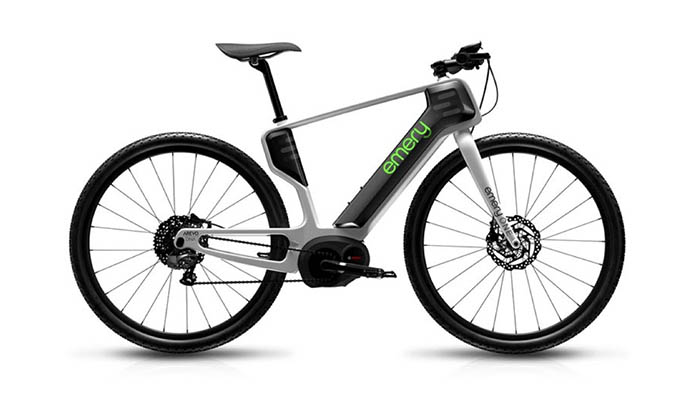
AREVO's bike frame was created using continuous fiber 3D printing | Credits: AREVO
Applications of composite materials
Being able to print with reinforcing materials has been the goal of many startups in the 3D printing industry. In recent years, we have seen a growing number of machines and technologies launching on the market to enable new applications, especially in industries such as aerospace and automotive. As mentioned, carbon fiber is one of the most widely used composite materials in 3D printing, especially for demanding applications such as functional prototypes, car parts, and strong yet lightweight components. As a result, carbon fiber composites are also becoming increasingly popular in the sports industry. Elite athletes are using carbon to create lighter and therefore faster bicycles. These advantages are also being exploited in Formula 1, the automotive industry, and even in sports such as tennis and rowing.
The composites market is growing and new material combinations will enable new applications. Engineering materials are exploring the use of additive reinforcement components. In China, researchers have studied the benefits of adding carbon fibers to high-performance thermoplastics such as PEEK, while Sandvik created the first diamond composite in 2019. Diamond cannot normally be used in additive manufacturing because it is too hard. However, by creating a diamond composite, the material properties can be used for many hard tools (mining, drilling or machining) and even medical implants!
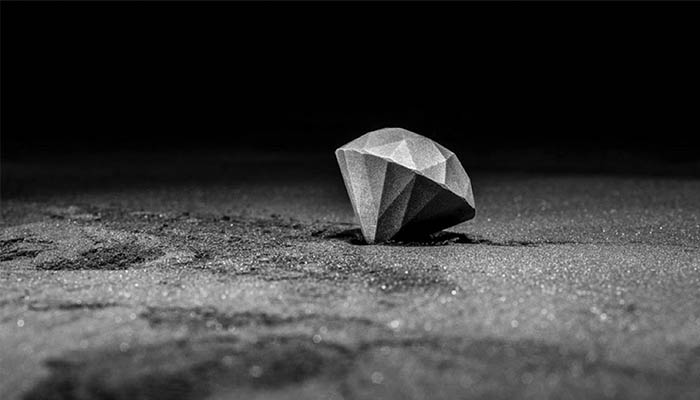
The composite diamond created by Sandvik
Composite Filament Manufacturers and 3D Printers
Of course, composite materials tend to be more expensive than standard materials. However, prices vary depending on the manufacturer and the composite used. The price of a roll varies from 150 to 500 euros. A composite material also requires a printer with special properties for its use. Such printers often have their own technology, which is described and marketed differently by the manufacturers. Markforged, for example, has developed the CFF (Continuous Carbon Fiber) technology for the composite printers it offers. Anisoprint has called it CFC (Continuous Fiber Coextrusion). A well-known name that is added to the list of composite printers is Stratasys. With the F190 CR and F370 CR 3D printers, Stratasys has expanded the F123 series to offer printers compatible with composite materials, especially those with high stiffness and strength.
Another interesting technology is the one patented by AREVO. It is based on the directional energy delivery technique, which uses a laser to simultaneously heat the filament and the carbon fiber while a roller presses them together. The Swiss company 9T Labs, for example, has developed a complementary system for regular 3D printers that allows 3D printing of composite materials. This 3D printing process is called AFT (Additive Fusion Technology). Finally, Continuous Composites uses a hybrid technology in which the fiber yarn is impregnated with resin and then cured with UV light, similar to SLA 3D printing.
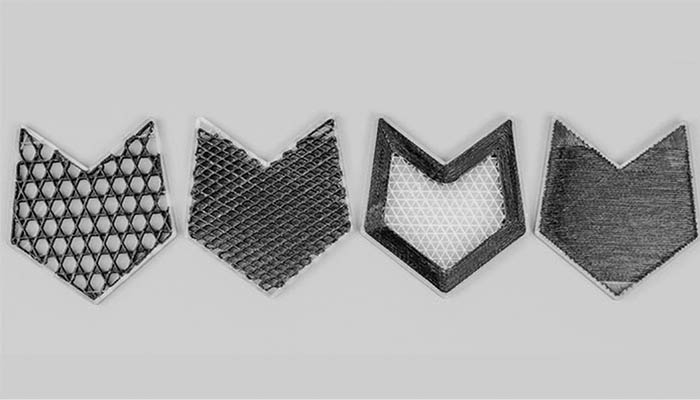
Anisoprint software can generate many types of continuous fiber reinforced infills.
Among the composite filament manufacturers, there are also well-known names. Markforged offers glass fiber composites and Kevlar. Owens Corning is also known for its glass fiber reinforced materials. Formfutura, BASF and XYZPrinting have also added composite filaments to their range. Among the short fiber composites, filament manufacturers Roboze, 3DXTech and ColorFabb stand out.